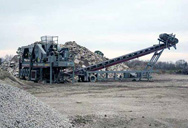
The Sintering Process of Iron Ore Fines – IspatGuru
The Sintering Process of Iron Ore Fines. Sintering plants are normally associated with the production of hot metal in blast furnaces in integrated steel pants. The process of sintering is basically a pre-treatment process step during iron making for the production of the charge material called sinter for the blast furnace from iron ore fines and also from metallurgical wastes (collected dusts, sludge and mill scale …
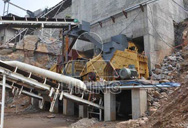
The Sintering Process of Iron Ore Fines IspatGuru
Similar to sintering, pelletizing is another widely used process to agglomerate the iron ore. Sinter plants are usually located near the blast furnace plant, but pelletizing plants are often located near the mining site. Some works have both pelletizing and sintering plants at the smelter sites.
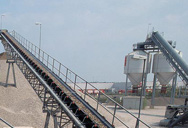
Iron Ore Sintering For Blast Furnace
Iron Ore Sintering For Blast Furnace. In theory, any ore containing iron or iron compound can be called iron ore used for steel making processere we introduce some iron ore magnetite is an iron ore, the main ingredients is fe3o4he color is dark gray, containing fe72, o 27agnetic method can be used during beneficiation in steel making by using nickel smelter.
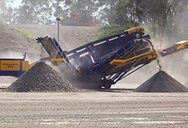
Iron ore sintering consumation in blast furnace
Blast furnace Produces pig iron from iron ore and sinter The iron oxide of ore and sinter is reduced to iron with the help of carbon monoxideCo which is produced inside the furnace by the action of hot air at about 1000 oC with coke Another purpose of coke is to supply heat for reaction and melting iron inside the furnace. Oline Chat
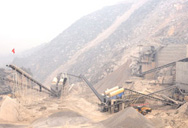
Sinter Into Iron Ore Blast Furnace - plaidwebshop.nl
In iron ore sinter plants blast furnace dust and other fine-grained residues which are rich in iron or car-bon content are recycled. The carbon contained in the blast furnace dust can be used to replace coke breeze which is added to the charge as fuel for the sintering process. However, there is no information in Iron ore sintering ScienceDirect
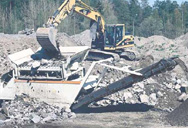
iron ore sintering for blast furnace
Blast Furnace Iron oxides can come to the blast furnace plant in the form of raw ore, pellets or sinter The raw ore is removed from the earth and sized into pieces that range from 05 to 15 inch This ore is either Hematite (Fe2O3) or Magnetite (Fe3O4) and the iron content ranges from 50% to 70%...
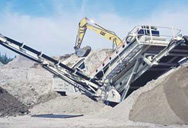
Iron Ore Pelletizing Sintering Mineral Processing …
These are typically fed to a blast furnace or DRI plant as part of the process to make steel. (PDF) Iron Ore Sintering: Process - ResearchGate. Sintering is a thermal agglomeration process that is applied to a mixture of iron ore fines, recycled ironmaking products, fluxes, slag-forming agents and solid fuel (coke). Iron Ore Pelletizing Process: An Overview | IntechOpen. The iron ore ...
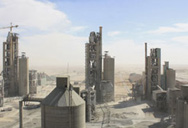
Sintering: A Step Between Mining Iron Ore and …
Sinter is the primary feed material for making iron and steel in a blast furnace. According to the U.S. Environmental Protection Agency, the sintering process converts fine-sized raw materials, including iron ore, coke breeze, limestone, mill scale, and flue dust, into an agglomerated product, sinter, of suitable size for charging into the blast furnace.
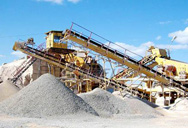
iron ore sintering furnace - …
Sintering of iron ore is a generic term which is used to describe the process whereby a sinter mix (raw mix or green mix) of iron ore fines fluxes fuel (coke breeze) and plant return fines (e g mill scale blast furnace dust and returned sinter fines etc) are converted into a particular form of
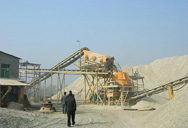
Sinter plant - Wikipedia
Sinter plants agglomerate iron ore fines (dust) with other fine materials at high temperature, to create a product that can be used in a blast furnace. The final product, a sinter, is a small, irregular nodule of iron mixed with small amounts of other minerals. The process, called sintering, causes the constituent materials to fuse to make a single porous mass with little change in the stone properties of the ingredients. The purpose of sinter are to be used converting iron into steel.
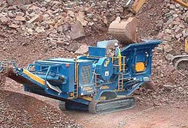
Blast Furnace Operation - an overview | …
The sintering process begins with the preparation of a sinter mixture consisting of iron ore fines, fluxes, solid fuel (called bonding agents in Japan) such as coke breeze, and return fines from the sinter plant and blast furnace as well as recycled ferruginous materials from downstream iron and steelmaking processes. After being mixed in a rotating drum, water is then added to the mixture. …
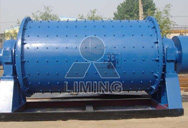
iron ore microfines sintering - klimaatwebsite.be
Iron ore sintering is used all over the world to prepare agglomerates for the ironmaking blast furnace , Figure 1 shows a schematic diagram of the major processes in a typical iron ore sintering plant The blended sinter mix – typically composed of iron ores, fluxes, returned sinter fines, plant dust and about 4 wt% coke breeze – is first granulated to coarsen its size distribution. 【Get ...
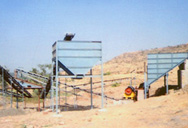
Iron Ore Sinter - an overview | ScienceDirect Topics
Sintering is the most economic and widely used agglomeration process to prepare iron ore fines for blast furnace use. Compared with pellets, production of sinter is cheaper, and compared with lump ore, fluxed sinter is often more reducible with better softening characteristics. Iron ore sinter typically constitutes more than 60% of the blast furnace ferrous burden in modern blast furnaces in ...
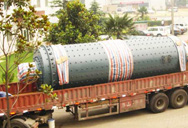
Iron Ore Sintering For Blast Furnace - Meipaly …
Iron ore sintering ScienceDirect. Sintering is the most economic and widely used agglomeration process to prepare iron ore fines for blast furnace use In this chapter the sintering process is first described and the key steps of the sintering process namely granulation and thermal densification are …
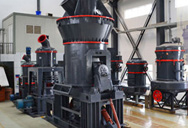
iron ore minning blast furnace for sale - …
Iron ore fines market in India news.steel-360. Odisha ban on iron ore fines sale has been in Karnataka and Goa alleged for illegal mining fed directly into Iron-making Blast Furnace.
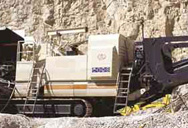
Blast Furnace – Official Minecraft Wiki
Blast furnaces are similar to furnaces, but can smelt only ore blocks and tools/armor made of iron, gold or chainmail. Smelting equipment yields one iron or gold nugget from their respective materials. Once an item and a fuel are placed into the blast furnace, the block state changes to lit and the item is smelted twice as fast as a regular furnace. Fuel is also used at double the rate of ...
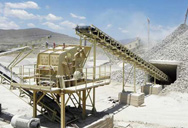
Blast Furnace Operating Conditions Manipulation …
A comparative reduction behavior of wüstite samples prepared from iron ore sinter was investigated to find the optimum way for reducing coke consumption and CO 2 emission in blast furnace technology. A series of wüstite reduction experiments was carried out using different gas mixtures. A correlation between the experimental results and real data of blast furnaces at Egyptian Iron and Steel ...
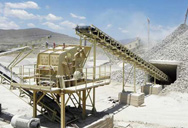
iron ore pellets versus sinter in blast furnace
Iron ore (pellet, sinter and lump ore) is gradually reduced to iron in blast furnace The reductions are a serial of heterogeneous gas solid reactions that take place from the top of the furnace and throughout the shaft region of the furnace
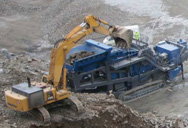
Iron Ore | ScienceDirect
Sintering is the most economic and widely used agglomeration process to prepare iron ore fines for blast furnace use. In this chapter, the sintering process is first described and the key steps of the sintering process, namely, granulation and thermal densification, are identified. Discussion is then focused on the effect of the chemical, physical, and mineralogical characteristics of iron ore on these steps and the …