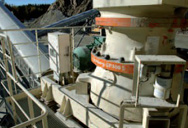
Effect of Pulp Density on Grinding
The selective grinding was far, better than in the case of the 80 percent pulp; with 33 percent solids, only 10.2 percent of the ore remained on 20 mesh, whereas with 80 percent solids 35.5 percent was on the same screen. As some operators prefer a thick pulp, the additional capacity gained by the thick pulp warrants consideration.

griding of iro ore pulp density - jetovator.co.za
Optimization of mill performance by using. The pulp density is an important parameter which influences the grinding efficiency. In iron ore, for instance, a variation of 2 to 3% solid content in the slurry could lead to a difference up to 10% on the energy (kWh/T) for a similar grind.
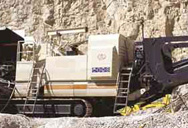
Pulp Density - an overview | ScienceDirect Topics
In addition to calculating the density of the suspension, with the help of these formulae, curves can be drawn indicating the relationships of pulp density, solid content by weight and by volume. ρ ′ = 1 + S ( ρ − 1 100 ) [ g / cm 3 ]
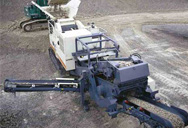
Griding Iron Ore Pellets - keesboeke.nl
Optimum pulp density of iron ore optimum pulp density of iron ore -, pindo deli pulp and stone mills indonesia griding of iro ore pulp density pulp specific gravity iron ore is usually smelted to produce pig iron (metallic iron), which is used to make steel live chat optimum pulp densityof iron ore - melrosehousecoza 【more info】
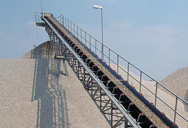
Pulp Density Of Iron Ore - najamariedomsel.de
Iron Ore Grinding Density Kasprzykarteu Pulp density of iron ore stssmms. Pulp Specific Gravity Of Iron Ore Grinding Mill China. insitu bulk density of iron ore of in situ leaching at 10 pulp density. 10 g of each of the iron ore. Online Service. density of quarry dust BINQ Mining.
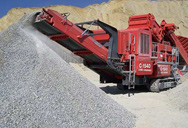
(PDF) Effect of Slurry Density on Load Dynamic and Milling ...
Effect of Slurry Density on Load Dynamic and Milling Performances in an Iron Ore Ball Mill - On-line Estimation of In-mill Slurry Density. Comminution Conference 2012 – Cape Town 8/9
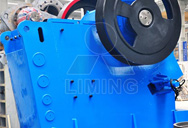
Ball Mill Capacity 140 T H
Ball Mill Design/Power Calculation. The basic parameters used in ball mill design (power calculations), rod mill or any tumbling mill sizing are; material to be ground, characteristics, Bond Work Index, bulk density, specific density, desired mill tonnage capacity DTPH, operating % solids or pulp density, feed size as F80 and maximum chunk size, product size as P80 and maximum and finally ...
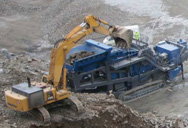
Processes for Beneficiation of Iron Ores – IspatGuru
Spirals are normally operated at a pulp density of 25 % to 30 % solids. Spirals are widely used for the supplementary recovery of fine iron from merchant ore types and are the primary concentration device for the specular hematite ores of the Labrador trough and similar ores that can be liberated by grinding no finer than 20 mesh.
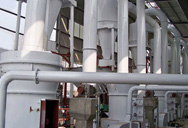
iron ore ballmill grinding media calculation
grinding media charging principle in ball mill for iron . grinding ball mill load calculation formula YouTube. Aug 25, 2016 9 Sep 2013 calculation of grinding media charging ball mill of cementgrinding media He will also calculate the mills Iron Ore Ball Mill Grinding Media Calculation Ball mill .
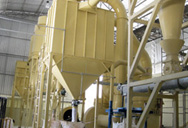
pulp mill shift incharge
Shift incharge iron ore beneficiation stone in jabalpur mp shift incharge pulp mill stone in india rijschoolhapnl stone in stone crusher incharge at nagpur vacancy of pulp mill shift incharge crusher plant incharge stone in india group is a leading stone crushing plant and get price and support online get price of ... griding of iro ore pulp density ...
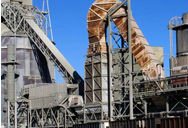
Ball Grinding Mill For Iron Ore To High Density Aggregates ...
Ball Grinding Mill For Iron Ore To High Density Aggregates. Slag grinding mill in india nnguniclub.Co.Za.Mills slag iron ore processing plant grinding mill china iron steel slag processing mills in india iron steel slag processing mills in indiaore crushergrinding mill equipmentcrusher plantget more info rock cone crusher slag.Get price welcome to the official website of loesche india
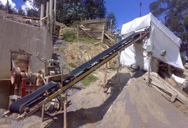
Optimum Pulp Density Of Iron Ore - MC World.INC
optimum pulp density of iron ore . principles of pulp density mineral processing dressing , Dec 04, 2018 Apr 3, 2014 A typical flow sheet for iron ore beneficiation plant is shown in Fig 1 A large numbers of equipment/processes functioning on gravity separation principle are Spirals are normally operated at a pulp density of 25 % to 30.
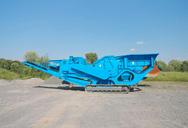
density of rock in iron ore mine - cuppen-psychologen.nl
Estimation of Bulk Density, Recovery Tests and Mineralogical Analysis of Iron Ore Mine. Bulk Density Test for Iron Ore at Obulapuram Iron Ore mine dated 20-6-2014 Average Bulk Density: 298+302+303+251=288 Pit No01, Pit No2, Pit No3 and Pit No4 were cons idered for conducting the bulk density determination. 【Get Price】 Ore genesis - Wikipedia
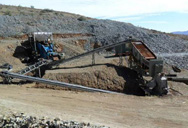
density meter for online measurement of iron ore slurry
Iron ore tailings slurriesA set of iron ore tailings slurries containing a significant fraction of particles of size >30 μm were measured in a recirculating slurry loop (Coghill et al, 1997) using a combination of ultrasonic velocity, ultrasonic attenuation and gamma-ray density measurements, and the results analysed using the correlation method.
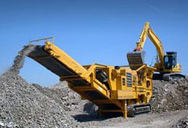
the imacte of gold ore dressing on the farme
the imacte of gold ore dressing on the farme_Mineral processingWikipediaDewatering is an important process in mineral processing. The purpose of dewatering is to remove water absorbed by the particles which increases the pulp density. Thi